Technology
Double-sided patch coating
Conventionally, a layer of platinum-based catalyst is coated onto the entire surface of a PEM (polymer electrolyte membrane) on both sides to form a CCM (catalyst coated membrane); much of this expensive catalyst is covered when the CCM is mounted into a frame, rendering it effectively useless as it cannot interact with the reaction area. SinoHyKey has been able to cut down on the amount of catalyst wasted by selectively coating the PEM, reserving this precious resource only for the parts that need it. Through PGM loading reduction and yield improvement, the roll-to-roll direct coating technology has been able to reduce the cost of CCM and MEAs effectively. SinoHyKey’s proprietary ink preparation and coating techniques, as well as our computerized screening process, ensure a flawless catalyst consistency with minimal aggregation and cracking.
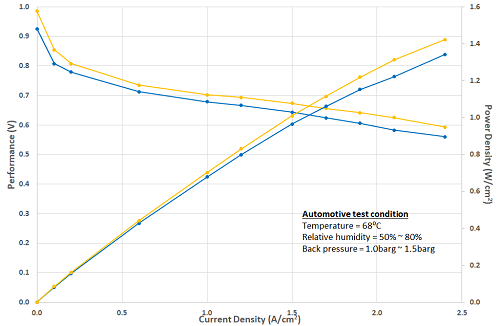
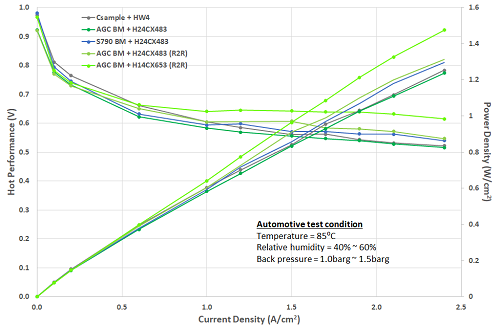
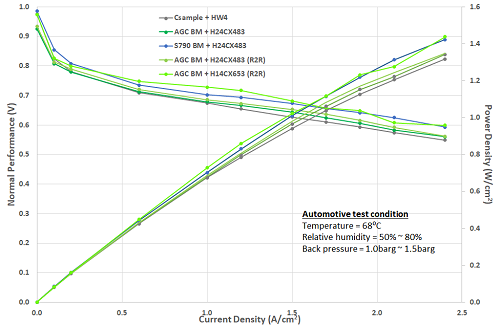
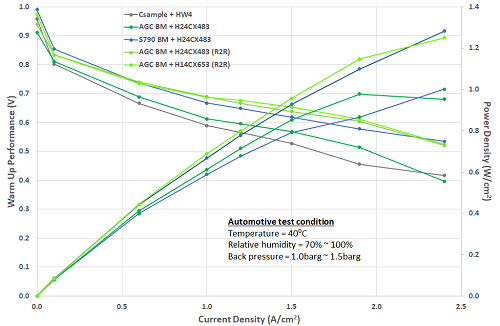
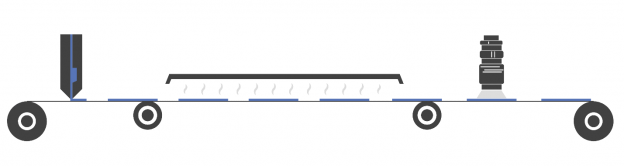
SinoHyKey cathode coating process

SinoHyKey anode coating process
Quality control technology
- CCM/ink inspection: prior to coating, the catalytic ink is checked for rheology, particulate size, structure, and performance using specialized equipment like the DV3T rheometer and laser particle size analyzer. After the ink is deposited onto the PEM, the dimensions, catalyst loading, electrochemical and mechanical characteristics of the resulting CCM are verified. The product is then assigned a grade from A to D based on the degree of cracking in the catalyst layer; only the highest ranked CCMs are provided to customers, while the rest are discarded or used for testing.
SEM images of A to D grade CCMs
- MEA inspection: after the CCM is cut and assembled into the MEA, this final piece must be free of leakages and its dimensions within the accepted tolerances; any MEAs that do not meet requirements are marked for further examination. The images below show the assembled MEA undergoing a dimensional inspection.
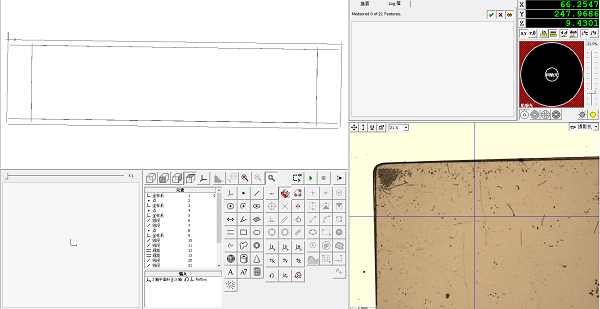
MEA dimensional inspection process
OER technology
A fuel cell functions normally when the anode and cathode reactions both have access to an appropriate supply of electrons and protons. However, during operation, factors such as rapid changes in electrical load or insufficient reactant flow can upset this delicate balance, resulting in an increase in anode potential and a decrease in cathode potential. If adequately extreme, this can lead to a phenomenon known as cell reversal, causing irreparable damage to the MEA; therefore, measures must be taken to prevent this from occurring.
One solution that SinoHyKey is developing is a special catalyst to be used at the anode, the purpose of which is to encourage the neutral oxygen evolution reaction (OER), rather than the damaging carbon oxidation reactions (CORs). With this technology, MEAs can last longer and become more reliable, removing one of the major obstacles to fuel cell commercialization.
Testing technology
In order to simulate MEA performance under real-world conditions, we use several test stations to evaluate our products as part of both single cell and short stack configurations. In our fully equipped electrochemistry lab, our engineers verify the quality of our products by modelling real-time PEMFC operating parameters and degradation mechanisms – this allows us to study the durability of our MEAs and CCMs in a stack and potentially improve upon our OER figures. In this way, we guarantee that only the best products are delivered to our valued clients.
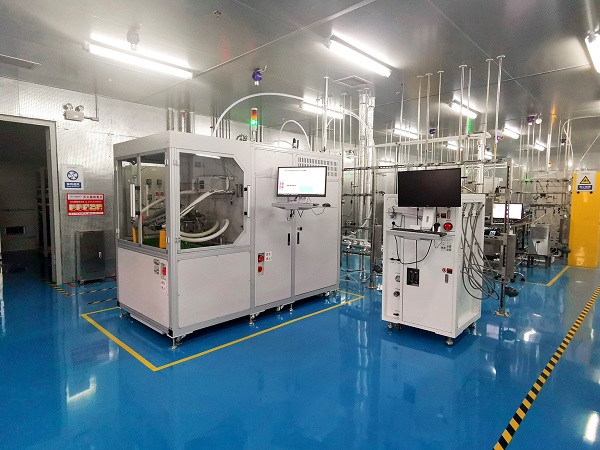
SinoHyKey MEA testing and validation lab
Quality management
We are proud to offer solutions that we believe to be of the utmost quality – this is ensured by numerous checkpoints in the manufacturing process where we employ state-of-the-art equipment to ensure that each product meets our demanding standards of performance and reliability. SinoHyKey obtained ISO9001:2015 quality management system and IATF16949:2016 automotive quality system certification in 2022. Through the comprehensive quality system, we standardized manufacturing processes to ensure production stability and to reduce waste due to material- and process-related deficiencies. We strive to provide our customers with reliable solutions, continuously improve customer satisfaction, and achieve win-win results.